فهرست مطالب
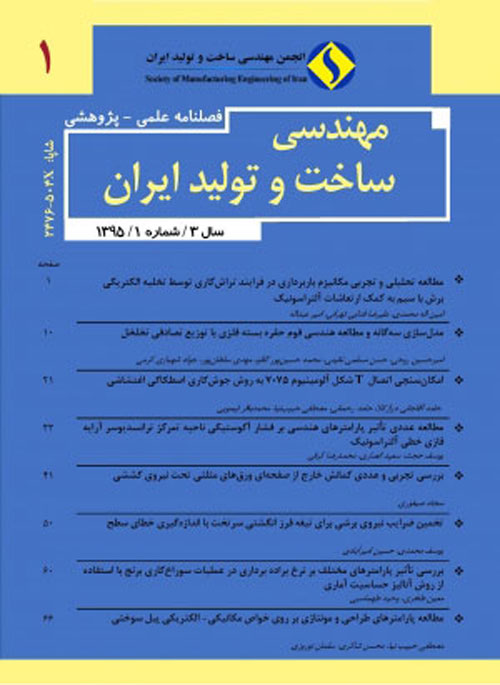
مجله مهندسی ساخت و تولید ایران
سال ششم شماره 4 (مهر 1398)
- تاریخ انتشار: 1398/07/01
- تعداد عناوین: 6
-
-
صفحات 1-6
هدف از این مطالعه بررسی تاثیر استفاده از ابزار ماسوره ای بر روی خواص مکانیکی اتصال آلیاژ آلومینیوم 6061-T6 در جوشکاری اصطکاکی اغتشاشی می باشد. روش جوشکاری اصطکاکی اغتشاشی یکی از روش های مناسب جوشکاری آلیاژهای آلومینیوم جهت کاهش عیوب جوش و افزایش استحکام اتصال می باشد. در این فرایند علاوه بر پارامترهای جوشکاری از جمله سرعت دورانی و سرعت پیشروی، نوع و هندسه ابزار نیز تاثیر بسیاری زیادی بر کیفیت و استحکام جوش دارد. در این مطالعه با استفاده از ابزار معمولی و ابزار ماسوره ای، تاثیر نوع ابزار و پارامترهای جوشکاری بر استحکام مکانیکی اتصال مورد بررسی قرار گرفته است. نتایج بدست آمده از این مطالعه نشان می دهد که ابزار ماسوره ای نسبت به ابزار معمولی کارایی و توانمندی بالاتری در اتصال این نوع آلیاژ دارد. از مهمترین ویژگی های این ابزار نسبت به ابزار معمولی امکان جوشکاری هر دو سمت ناحیه اتصال در یک مرحله از جوشکاری می باشد. همچنین از لحاظ استحکام مکانیکی اتصال، استفاده از ابزار ماسوره ای منجر به بهبود استحکام کششی اتصال و مقاومت به ضربه بهتر جوش شده است. بررسی تاثیر پارامترهای جوشکاری نشان می دهد که با افزایش سرعت دورانی ابزار از 900 به 1100 دور در دقیقه و نیز افزایش سرعت پیشروی ابزار از 25 به 32 میلیمتر بر دقیقه استحکام برشی اتصالات افزایش یافته است.
کلیدواژگان: جوشکاری اصطکاکی اغتشاشی، آلومینیوم 6061-T6، ابزار ماسوره ای، استحکام مکانیکی، شکست -
صفحات 7-13امروزه استفاده از قطعات فلزی روکش داده شده بدلیل خواص قابل توجهی که نمی توان از مواد تک لایه بدست آورد، در بسیاری از صنایع به سرعت در حال گسترش است. در این پژوهش تولید میله آلومینیومی AA7075 با روکش مس خالص به روش اکستروژن مستقیم داغ مورد بررسی قرار گرفته است. جهت دستیابی به کیفیت مطلوب اتصال، اکستروژن مستقیم داغ در حالت های مختلف انجام شد و در نهایت آزمایش اصلی با زاویه قالب 45 درجه، نسبت اکستروژن 4 و دمای 480 درجه سلسیوس انجام گرفت. به منظور بررسی خواص مکانیکی میله روکش داده شده آزمون کشش بر میله آلیاژ آلومینیوم، مس خالص و میله اکستروژن داغ شده دو لایه Al-Cu انجام گرفت. همچنین میکروسختی و میکروساختار آلومینیوم روکش شده بررسی شد. نتایج نشان داد که با استفاده از فرآیند اکستروژن مستقیم داغ می توان میله آلومینیومی با روکش مس تولید کرد که ضمن حفظ خواص الکتریکی و حرارتی، خواص مکانیکی و نسبت استحکام به وزن مطلوب، از کیفیت اتصال مناسب نیز برخوردار باشد. تصاویر میکروسکوپی نشان داد که متوسط ضخامت لایه مرزی اتصال آلومینیوم و مس حدود 22 میکرون است، ضمن اینکه از کیفیت و سختی قابل قبولی نیز برخوردار می باشد که نشان دهنده نفوذ و در هم تنیدگی مناسب دو جنس در یکدیگر می باشد. همچنین نتایج نشان داد میله روکش داده شده از استحکام تسلیم، نهایی و همچنین شکل پذیری خوبی در مقایسه با هر کدام از میله های تک لایه مورد استفاده برخوردار می باشد که حاکی از کیفیت مناسب میله روکش دار می باشد.کلیدواژگان: میله دو لایه، آلیاژ آلومینیومAA7075، مس خالص، اکستروژن داغ، خواص مکانیکی
-
صفحات 14-22در سال های اخیر روش های مختلفی برای تولید لوله های چهارگوش بوسیله فرآیندهای شکل دهی مجدد ارائه گردیده است. به طور عمده انتظار می رود که شکل دادن یک لوله مربعی برای استفاده صنعتی بدون عیب باشد، که این موضوع باید در مرحله طراحی و قبل از شروع آزمایشات عملی، بررسی شود. در این مقاله تغییر شکل الاستیک-پلاستیک یک لوله گرد فلزی طی فرآیند شکل دهی مجدد غلتکی سرد و تبدیل آن به لوله بدون عیب با مقطع مربعی توسط نرم افزار اجزاء محدود اباکوس بررسی شده است. میزان شکل گیری عیب تورفتگی(پارامترC) در قسمت تخت لوله چهارگوش در طول فرآیند شکل دهی یکی از موارد موثر در کیفیت نهایی این لوله ها به حساب می آید. بر این اساس، در این تحلیل اثر پارامترهای مختلف فرآیند مانند نسبت هندسی، مقدار کاهش ارتفاع، ضریب اصطکاک، شعاع غلتک و جنس لوله ها بر روی میزان رخ دادن عیب تورفتگی در فرآیند چهارگوش کردن مورد بررسی قرار گرفته است. یافته ها نشان می دهد که با افزایش کاهش ارتفاع، مقدار پارامترC برای نسبت های هندسی ثابت افزایش می یابد. نسبت هندسی به عنوان یک عامل مهم در میزان شکل گیری پارامتر C می تواند نقش مهمی را در فرآیند چهارگوش کردن لوله داشته باشد. به منظور تایید نتایج حاصل از شبیه سازی یکسری آزمایش های تجربی انجام گرفت که تطابق خوبی بین نتایج شبیه سازی و آزمایش های تجربی مشاهده گردید.کلیدواژگان: شکل دهی مجدد غلتکی سرد، عیب تورفتگی، روش اجزاء محدود، لوله چهارگوش
-
صفحات 23-28در این پژوهش تحقیقاتی؛ از روش آلیاژسازی مکانیکی به همراه تف جوشی پسین به منظور تولید و فرآوری مکس فازهای پایه زیرکونیم با ریزساختار نانوکریستالی بهره گرفته شده است. برای نیل به این مقصود؛ مقادیر مشخصی از ترکیبات عنصری با خلوص بالای اولیه با نسبت شیمیایی مشخص شامل هیدرید زیرکونیم، آلومینیم و گرافیت در دستگاه با انرژی بالای آسیاب مکانیکی سیاره ای برای مدت زمان های مشخص (5، 10، 20، 40 و 60 ساعت) تحت فرآیند خردایش و آسیاب قرار داده شد. ترکیبات فرآوری شده با استفاده از طیف سنجی پرتو ایکس (XRD)، مشاهدات میکروسکوپ الکترونی روبشی (SEM) و آزمایشات سختی سنجی مورد مطالعه واقع شد. نتایج آزمایشگاهی مشخص ساخته است که پس از 40 ساعت آسیاب؛ مکس فاز Zr2AlC با اندازه بلوریت پایین تر از 25 نانومتر و سختی قابل ملاحظه 971 ویکرز پدیدار می گردد. همچنین با افزایش زمان آسیاب کاری مورفولوژی ذرات تولید شده از حالت لایه ای به کروی تغییر می یابد. تف جوشی پودرهای آسیاب شده برای مدت زمان 2 ساعت و در دمای 1300 درجه سانتی گراد، پیدایی مکس فازهای Zr3AlC2 و Zr4AlC3؛ رشد دانه و افزایش اندازه بلوریت و همچنین رهایش کرنش های داخلی را به دنبال خواهد داشت. با توجه به نتایج به دست آمده مشخص می گردد که فرآیند به کار گرفته شده (آسیاب مکانیکی و تف جوشی)، روشی سودمند، مقرون به صرفه و پر بازده برای تولید مکس فازهای پایه زیرکونیم با ساختار نانومتری و مورفولوژی همگن به شمار می رود.کلیدواژگان: مکس فاز، مکانیسم فرآوری، فناوری پودر، نانوبلور
-
صفحات 29-36فرآیند داخل تراشی به دلیل نسبت طول به قطر بالای ابزار و انعطاف پذیری زیاد آن، بسیار مستعد ارتعاشات خود برانگیخته(لرزش) است. تاکنون روش های مختلفی جهت افزایش سفتی دینامیکی ابزارها بکارگرفته شده است که موثرترین آنها روش های کنترل فعال هستند. برای تحلیل و طراحی سیستم کنترلی به مدل دینامیکی سیستم نیاز است. با توجه به اینکه بدست آوردن مدل سیستم با استفاده از روش های معمول مدلسازی اجزای محدود پیچیده و زمانبر است، بنابراین روشی که بتواند به سرعت و با دقت بالا پاسخ سیستم کنترل ارتعاشی را تخمین بزند از کارایی بالایی برخوردار است. هدف از این پژوهش، ارائه روشی برای مدلسازی دینامیکی ابزار داخل تراش با استفاده از تحلیل مودال تجربی است که بتوان با استفاده از آن عملکرد کنترلر را در کاهش ارتعاشات شبیه سازی و پیش بینی نمود. در این روش ابتدا با استفاده از آزمون مودال تجربی یک مدل ماتریسی خطی از دینامیک سیستم استخراج گردیده و سپس با استفاده از روش جاروب سینوسی مدل عملگر-ابزار شناسایی می گردد. در ادامه با استفاده از مدل های بدست آمده، حلقه کنترل فعال ارتعاشات ابزار داخل تراش در محیط نرم افزار متلب/سیمولینک شبیه سازی شده و عملکرد کنترلر بررسی گردید. در انتها نیز نتایج شبیه سازی با نتایج آزمایشگاهی مقایسه گردید که نشانگر عملکرد مناسب روش پیشنهادی برای مدلسازی دینامیکی سیستم و طراحی کنترلر می باشد. روش ارائه شده در دامنه فرکانسی شناسایی شده به خوبی پاسخ سیستم را تخمین می زند و با استفاده از این روش می توان ضریب بهره کنترلر را بهینه نمود.کلیدواژگان: ابزار داخل تراش، آزمون مودال تجربی، مدلسازی دینامیکی، شبیه سازی، کنترل فعال ارتعاشات
-
صفحات 37-51یکی از مهم ترین عوامل اثرگذار بر خواص مکانیکی، فیزیکی و شیمیایی فلزات، اندازه دانه می باشد. فلزات فوق ریزدانه دارای میانگین اندازه دانه 1000-100 نانومتر و فلزات نانوساختار داری میانگین اندازه دانه کمتر از 100 نانومتر هستند. مواد فوق ریزدانه و نانوساختار به عنوان نسل جدیدی از محصولات فلزی شناخته می شوند که در مقایسه با فلزات درشت دانه دارای خواص مکانیکی و فیزیکی قابل ملاحظه ای هستند. در دودهه ی اخیر، به دلیل خواصی نظیر استحکام بالا، شکل پذیری و چقرمگی بالا، مقاوت به خوردگی خوب و خاصیت سوپرپلاستیسیته بالا، ساخت این مواد مورد توجه بسیاری از محققین قرار گرفته است. در سال های اخیر، روش های زیادی تحت عنوان تغییر شکل پلاستیک شدید ارائه شده است و هم اکنون نیز در حال تکامل و گسترش می باشند. در این فرآیندها، با وجود فشار هیدرواستاتیکی بالا و عدم تغییر ابعاد نمونه در حین فرآیند، امکان اعمال کرنش های بسیار بالا میسر می شود که متعاقبا خواص مکانیکی مطلوب و مواد فوق ریزدانه و نانوساختار حاصل می شود. فرآیند نورد تجمعی یکی از روش های تغییر شکل شدید پلاستیک می باشد. فرآیند نورد تجمعی روشی پرکاربرد، ساده، کم هزینه با قابلیت صنعتی می باشد که توانایی تولید فلزات فوق ریزدانه و نانوساختار را دارد. در این تحقیق فلزات سبک نظیر آلومینیوم، منیزیم و تیتانیوم و همچنین فلزات پرکاربرد مس و فولاد مورد بحث قرار می گیرد. همچنین خواص مکانیکی، شکست نگاری و ویژگی های ریزساختاری فلزات فوق ریزدانه و نانوساختار تولیدشده به روش نورد تجمعی با نمونه های اولیه مقایسه می شود و مکانیز های حاکم بر فرآیند نورد تجمعی که باعث تغییرات خواص مکانیکی و ریزساختاری می شود مورد تحلیل قرار می گیرد.کلیدواژگان: فلزات فوق ریزدانه و نانوساختار، تغییر شکل پلاستیک شدید، نورد تجمعی، خواص مکانیکی و ریزساختاری
-
Pages 1-6
The purpose of this study is to investigate the effect of using bobbin tool on the mechanical properties of aluminum alloy 6061-T6 in friction stir welding. The friction stir welding method is one of the suitable process to welding aluminum alloys to reducing welding defects and increase joint strength. In this process, the welding parameters such as the rotational speed of tools and travel speed, beside the type and geometry of the tool also has a great effect on the quality and strength of the weld. In this study by using the typical tool and bobbin tool the effect of welding parameters on the mechanical strength of the welded joint are investigated. The results of this study show that the bobbin tool has a higher performance and capability in connection with this type of alloy. The main advantage of the bobbin tool is welding the both sides of the weld zone at one stage of the welding process compared to the typical tool. Also in terms of mechanical strength of connection, the use of bobbin tool has resulted in improving the tensile strength of the connection and resistance to a better impact. The effects of welding parameters show that by increasing the rotational speed of the device from 900 to 1100 rpm as well as increasing the travel speed of the tool from 25 to 32 mm/min of the joints shear strength has increased.
Keywords: Friction Stir Welding, Aluminum Alloy 6061-T6, Bobbin Tool, Mechanical Strength, fracture -
Pages 7-13The use of clad material as a structural material is increasing in many industries because it has material properties that cannot be obtained from a single material. For the present study, a hot forward extrusion process was applied to fabricate aluminum/copper (Al/Cu) clad composite rod. The different of extrusion ratios and die angles were applied to obtain the best extrusion condition. Finally, hot forward extrusion process was applied at a temperature of 480 ◦C with extrusion ratio of 4 and Die angle of 45 ⃘. The purpose of this paper was fabrication of Al-clad Cu rods by hot forward extrusion. Materials that used in this research were aluminum alloy of AA7075 and pure commercial copper as clad material. There were some experiments among pure copper, AA7075 (both without any extrusion and cold work) and Al-clad Cu rods that included Mechanical Tensile Tests, Micro Hardness tests and Microstructure compare. Microstructure characterizations of the Al/Cu interface and the neighboring regions revealed the formation of a suitable and adhesive bonded layer with thickness of 22 microns and acceptable Microhardness. The mechanical properties results of AA7075, copper and two layer Al/Cu rods reveal that the Yield strength, Ultimate Tensile strength and Formability of extruded Al/Cu rods are suitable in compare to single material rods consist of AA7075 and copper rods.Keywords: Two layer rod, Aluminum Alloy, Pure Copper, Hot extrusion, Mechanical properties
-
Pages 14-22In recent years, various ways have been used for productions of square tube by reshaping processes. Mainly, it is expected that forming of a square tube that does not have any defects for using in industrial application, should be investigated during the design stage, before trials begin. In this paper, the elasto-plastic deformation of a circular pipe into a square tube without any defects, during the cold re-shape rolling process, is examined by Abaqus finite element software. The occurrence of collapse defect (parameter C) in the flat part of square tube during the forming process is one of the influential negative factors in the final quality of these tubes. Accordingly, the effects of various process parameters such as geometric ratio, roll gap reduction, friction coefficient, roll radius and the material of the pipe, on the occurrence of collapse defect in the squaring process are discussed. The findings show that with increasing the roll gap reduction, the amount of parameter C increases for constant geometric ratios. The geometric ratio is a major factor on the occurrence of collapse defect in the process of squaring circular tubes. In order to verify the simulation results, several experimental tests were performed. Obtained results of simulation showed good agreements with the experiment results.Keywords: Cold Re-Shape Rolling, Collapse Defect, Finite element method, Square Tube
-
Pages 23-28In this research, the method of mechanical alloying and subsequent sintering has been used to obtain Zr-based MAX Phases compounds with nanocrystalline structure. For this purpose, a stoichiometric mixture of high purity elemental powders of ZrH2, Al and C (Graphite) was subjected to intense mechanical alloying in a planetary high energy ball mill under different milling conditions (5, 10, 20, 40 and 60 h). The fabricated compounds were characterized by X-ray diffractometry (XRD), scanning electron microscopy (SEM) and microhardness measurements. Experimental results exhibited that after an optimum milling time of 40 h, Zr2AlC MAX phase with the crystallite size of less than 25 nm and high microhardness of 971 HV can be obtained. Also with milling time, morphology of pre-alloyed powders changed from lamella to globular. Sintering of milled powders at 1300 °C for 2 h resulted in the production of nanometric Zr3AlC2 and Zr4AlC3 MAX phases, increase the crystallite size (grain growth), and release of internal strain. The results revealed that this route (high energy milling followed by sintering) is a powerful, cost effective and high productive technique for preparing Zr-based MAX phases compounds with nanometric structure and homogenies morphology.Keywords: MAX Phase, Production mechanism, Powder technology, nanocrystalline
-
Pages 29-36Due to the high length to diameter of the tool and its high flexibility, internal turning process is very prone to chatter vibrations. Different methods have been used to increase dynamic stiffness of tools; the most effective method is active control method. In order to analyze and design a control system, a dynamic model of the system is required. Obtaining a system model using finite element modeling technique is complicated and time-consuming, thus, a method that can quickly and accurately estimate the response of the vibration control system is very important. The aim of this study is to propose a method for dynamic modeling of the internal turning tool using the experimental modal analysis, which can be used to predict and simulate vibration reduction. In this method, using the experimental modal test, a linear matrix model of the system dynamics was extracted and then the actuator-tool model was identified using sweep frequency method. Thereafter, by using the obtained models, the active vibration control loop of the internal turning tool was simulated in MATLAB/SIMULINK software and the controller performance was investigated. Finally, the simulation results were compared with the experimental results, which indicate good performance of the proposed method for dynamic modeling of the system and controller design. The proposed method in the identification frequency range accurately estimated the system response, and this method can be used to optimize the controller's gain.Keywords: Internal turning tool, Experimental modal analysis, Dynamic Modeling, Simulation, active vibration control
-
Pages 37-51One of the most important factors affecting the mechanical, physical and chemical properties of metals, are crystal structure and grain size. Ultrafine metals with an average grain size of 1000-100nm and nanostructured metals have an average grain size of less than 100nm. Ultrafine and nanostructured materials are known as a new generation of metal products, which have remarkably mechanical and physical properties in comparison to coarse-grained metals. In the last two decades, due to good properties such as high strength, high ductility and toughness, good corrosion resistance and high superplasticity properties, these materials have been considered by many researchers. In recent years, many methods have been proposed for severe plastic deformation and are now being developed and expanded. In these processes, in spite of the high hydrostatic pressure and the unaltered dimensions of the sample during the process, it is possible to apply very high strains, which results in the desired mechanical properties and ultrafine grained and nanostructured materials. The accumulative roll bonding process is one of the methods of SPD. ARB process is simple, extensive use, low-cost, industrially capability method that can produce ultrafine and nanostructured metals. In this research, light metals such as aluminum, magnesium and titanium and also extremely used metal such as copper and steel are discussed. Also, mechanical properties, fractography and microstructural properties of ultrafine and nanostructured metals produced by ARB are compared with initial samples and the mechanisms governing of ARB process that cause changes in mechanical and microstructural properties are analyzed.Keywords: Ultrafine, nanostructure metals, sever plastic deformation, Accumulative Roll Bonding, mechanical properties, microstructure